What is Porosity in Welding: Crucial Tips for Getting Flawless Welds
What is Porosity in Welding: Crucial Tips for Getting Flawless Welds
Blog Article
The Scientific Research Behind Porosity: A Comprehensive Overview for Welders and Fabricators
Understanding the detailed mechanisms behind porosity in welding is important for welders and fabricators aiming for impressive workmanship. From the make-up of the base materials to the intricacies of the welding process itself, a wide variety of variables conspire to either exacerbate or reduce the presence of porosity.
Comprehending Porosity in Welding
FIRST SENTENCE:
Assessment of porosity in welding reveals vital insights right into the integrity and high quality of the weld joint. Porosity, characterized by the existence of dental caries or voids within the weld steel, is a common issue in welding processes. These gaps, if not properly addressed, can endanger the architectural stability and mechanical homes of the weld, resulting in potential failings in the ended up product.
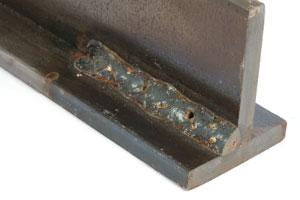
To identify and quantify porosity, non-destructive screening approaches such as ultrasonic testing or X-ray evaluation are often utilized. These techniques allow for the identification of internal defects without compromising the integrity of the weld. By assessing the dimension, shape, and circulation of porosity within a weld, welders can make enlightened decisions to enhance their welding procedures and achieve sounder weld joints.

Aspects Influencing Porosity Development
The event of porosity in welding is affected by a myriad of factors, ranging from gas securing efficiency to the complexities of welding criterion setups. Welding specifications, consisting of voltage, current, take a trip speed, and electrode kind, likewise influence porosity formation. The welding method employed, such as gas steel arc welding (GMAW) or shielded metal arc welding (SMAW), can affect porosity formation due to variations in warm distribution and gas insurance coverage - What is Porosity.
Results of Porosity on Weld Quality
Porosity development considerably endangers the structural stability and mechanical buildings of welded joints. When porosity exists in a weld, it produces gaps or dental caries within the material, minimizing the overall toughness of the joint. These voids act as stress and anxiety concentration points, making the weld a lot more prone to fracturing and failure under tons. The visibility of porosity likewise damages the weld's resistance to deterioration, as the entraped air or gases within the gaps can respond with the surrounding atmosphere, causing destruction over time. In addition, porosity can impede the weld's ability to withstand stress or influence, more endangering the general top quality and reliability of the welded structure. In important applications such as aerospace, automotive, or structural building and constructions, redirected here where security and sturdiness are extremely important, the destructive impacts of porosity on weld top quality can have severe consequences, emphasizing the significance of reducing porosity via correct welding methods and treatments.
Techniques to Lessen Porosity
To improve the top quality of bonded joints and make certain architectural stability, welders and producers use certain methods focused find out on decreasing the formation of gaps and tooth cavities within the product throughout the welding process. One efficient approach to reduce porosity is to guarantee correct product prep work. This includes complete cleaning of the base steel to get rid of any impurities such as oil, oil, or dampness that could contribute to porosity development. Furthermore, making use of the ideal welding specifications, such as the proper voltage, current, and travel speed, is crucial in protecting against porosity. Keeping a regular arc length and angle during welding likewise helps in reducing the likelihood of porosity.

Additionally, picking the ideal shielding gas and preserving proper gas flow prices are important in reducing porosity. Utilizing the proper welding strategy, such as back-stepping or utilizing a weaving motion, can additionally assist distribute warm equally and reduce the possibilities of porosity development. Making sure correct ventilation in the welding atmosphere to get rid of any type of prospective sources of contamination is important for achieving porosity-free welds. By carrying out these techniques, welders can properly decrease porosity and produce top notch welded joints.

Advanced Solutions for Porosity Control
Executing innovative technologies and innovative approaches plays a critical duty in accomplishing remarkable control over porosity in welding procedures. Furthermore, employing innovative welding strategies such as pulsed MIG welding or customized atmosphere welding can likewise help minimize porosity problems.
An additional innovative service entails making use of advanced welding tools. Using equipment with integrated features like waveform control and innovative power resources can enhance weld quality and he has a good point minimize porosity risks. The execution of automated welding systems with exact control over specifications can dramatically minimize porosity problems.
Moreover, including advanced monitoring and evaluation innovations such as real-time X-ray imaging or automated ultrasonic screening can assist in finding porosity early in the welding procedure, enabling immediate corrective activities. In general, incorporating these innovative services can significantly enhance porosity control and boost the general high quality of welded elements.
Final Thought
In verdict, understanding the scientific research behind porosity in welding is vital for welders and makers to produce premium welds. By recognizing the elements affecting porosity formation and executing strategies to minimize it, welders can enhance the general weld high quality. Advanced remedies for porosity control can better boost the welding procedure and ensure a solid and trusted weld. It is necessary for welders to continually enlighten themselves on porosity and execute finest techniques to accomplish optimum results.
Report this page